A paper bag making machine fabricates paper bags through a series of precisely engineered operations. It starts with the feed mechanism, moves on to cutting, shaping, and sealing processes, and concludes with applying finishing touches like handle attachment and printing. Let's explore this intricate process in detail.
1. The Initial Paper Feeding
1.1 Roll - Fed Machines
- In roll - fed setups, large - diameter rolls of paper, mainly made of kraft paper or recycled paperboard, are installed on the machine's unwind stand.
- A servo - controlled unwind system ensures the paper is unwound at a carefully regulated linear speed.
- High - precision tension sensors, often using load - cell or dancer - arm mechanisms, constantly monitor the paper tension. If there are any deviations from the set tension, the machine's control system quickly makes corrections. This might involve adjusting the unwind motor's speed or using braking systems to keep the paper feed steady. This stable paper feed is the basis for the following bag - making steps.
1.2 Sheet - Fed Machines
- For sheet - fed machines, pre - cut paper sheets are used. These sheets are fed into the machine one by one, usually through a vacuum - assisted or friction - driven feed system.
- Advanced sheet - fed machines have automatic sheet - alignment mechanisms. These use optical sensors or mechanical registration devices to accurately position each sheet before further processing. This high - precision alignment is very useful for making bags with different paper grades, thicknesses, or for creating custom - sized bags.
2. Cutting and Shaping the Bag
2.1 Cutting Operation
- Once the paper is fed, the cutting process begins. The machine uses rotary or reciprocating cutting tools, designed with specific shapes, to cut the paper into the right size and shape for the bag.
- For standard rectangular grocery bags, the paper is cut into rectangular pieces. For more complex bag designs, like gusseted bags with expandable sides, the cutting is more complex and requires precise cuts at specific angles and positions.
2.2 Shaping Process
- After cutting, the paper is turned into a three - dimensional form. Mechanical folding mechanisms, made up of cams, linkages, and pneumatic actuators, are used to fold and crease the paper.
- These components work together in a highly coordinated way, controlled by a programmable logic controller (PLC). The folding process is optimized to create sharp and well - defined folds, which are important for the bag's structural strength. For example, the bottom - folding mechanism is designed to make a strong base that can hold the weight of the bag's contents during transport and handling.
3. Sealing the Bag
3.1 Heat - Sealing Method
- Heat - sealing is a common sealing technique. Heat is applied to the bag's edges, usually using heated sealing bars or induction heating elements.
- The heat makes the paper fibers go through thermoplastic deformation, causing intermolecular bonding and creating a strong, leak - proof seal. Heat - sealing is popular because it can work at high speeds and is suitable for many types of paper, making it great for high - volume production.
3.2 Adhesive Sealing Method
- The other main sealing method is adhesive sealing. Food - grade adhesives, such as water - based or hot - melt adhesives, are used for the bag's seams.
- The adhesive is dispensed using precise metering systems, like gear pumps or slot - die coaters, to make sure it is applied accurately and evenly. This method is especially good for bags used for food packaging as it meets strict hygiene and safety standards. The adhesive bonds the paper layers together, providing a reliable seal while keeping the food product safe.
4. Adding Finishing Touches
4.1 Handle Attachment
- Handle attachment is a common finishing operation. Handles can be made from the same paper as the bag. In this case, the machine uses die - cutting and folding to create the handle shapes.
- These handles are then attached to the bag using adhesive or mechanical fastening methods like stapling. Handles can also be made from other materials like string or plastic. The machine has special attachment mechanisms to ensure the handles are firmly and durably connected.
4.2 Printing and Coating
- Printing is another important finishing step. The paper bag machine can use printing techniques such as flexography, gravure printing, or digital printing.
- Flexography uses a flexible relief plate to transfer ink onto the paper. The plate is on a printing cylinder, and an anilox roller system applies the ink. This allows for high - quality printing of detailed logos, brand names, and marketing messages.
- Gravure printing involves etching the image onto a metal cylinder, which is then filled with ink and transfers it to the paper.
- Digital printing has the advantage of on - demand, variable - data printing, allowing for highly customized designs.
- Additionally, some machines can apply special coatings, like varnishes or laminates, to improve the bag's look and durability.
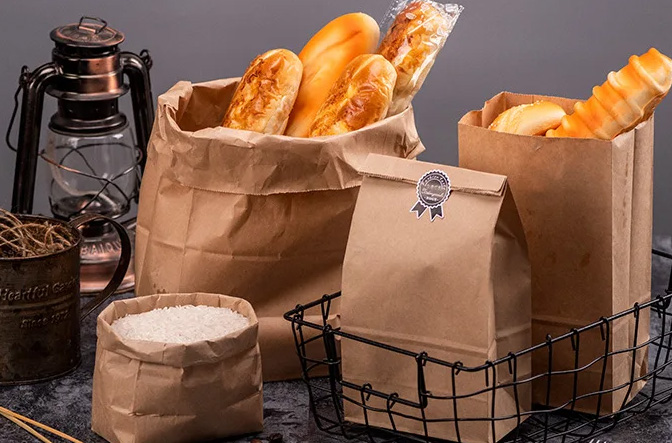
In conclusion
A paper bag making machine combines mechanical, electrical, and control engineering principles. From the precise paper - feeding to the detailed cutting, shaping, sealing, and finishing operations, each step is carefully designed to make paper bags that meet the various needs of the packaging industry. Whether it's a simple grocery bag or a high - end luxury gift bag, the paper bag making machine is key to turning raw paper into useful and good - looking packaging solutions.